Since its introduction in the 1960s, laser technology has rapidly developed into a key tool in industrial manufacturing due to its high energy density, good directionality and controllability. Compared with traditional mechanical processing methods, laser processing has the significant advantages of non-contact, high precision, high degree of automation, etc. It is widely used in industrial manufacturing such as material cutting, welding, marking, drilling, and additive manufacturing. According to the type of laser and its process characteristics, industrial laser processing is mainly divided into three categories: laser cutting, laser welding and laser additive manufacturing, each of which has its own unique mechanism and scope of application.
1.laser cutting
Laser cutting is one of the most mature industrial laser applications, using a high-power laser beam to melt and vaporize the material and an auxiliary gas to blow away the slag to achieve efficient and precise cutting.CO₂ lasers and fiber lasers are currently the mainstream equipment for cutting thin and medium-sized sheets of carbon steel, stainless steel, aluminum alloys and other materials. The advantages of this technology lie in the narrow kerf, small heat-affected zone, no need for molds and quick change of processing path, which is particularly suitable for automobile manufacturing, sheet metal processing and aerospace and other demanding industries.
(1) In automotive manufacturing, laser cutting is used to produce a wide range of components from body panels to engines. For example, fiber lasers are used to cut high-strength steel parts with high precision, resulting in lighter weight vehicles.
(2) The aerospace industry also benefits from laser cutting technology, particularly in the production of complex components made from advanced materials such as titanium and composites. For example, ultrafast lasers can be used to cut titanium components with complex shapes while minimizing thermal damage and ensuring the structural integrity of the component, significantly improving the performance and safety of aerospace components.
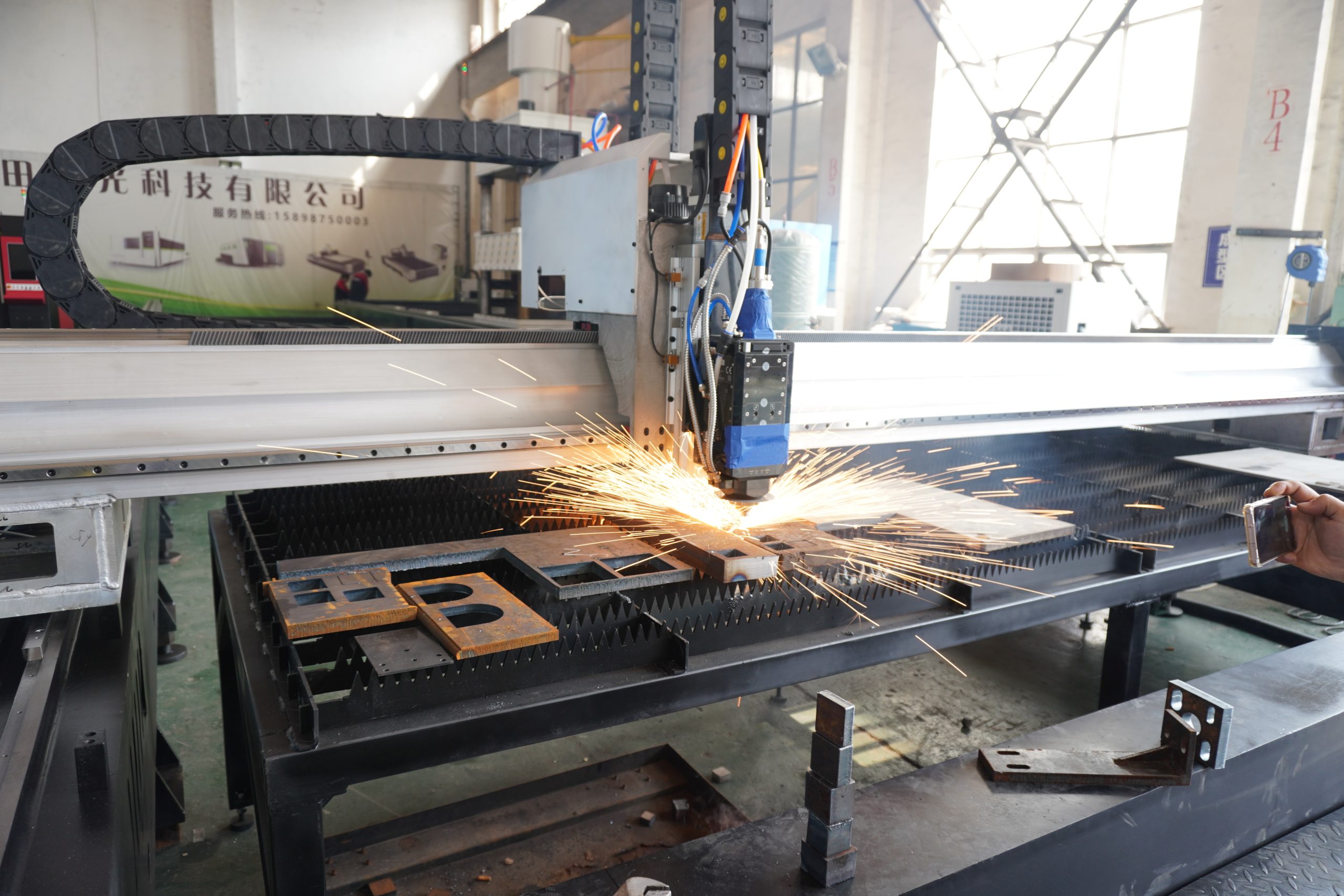
2.laser welding
Laser welding relies on a laser beam to melt metal materials at high speed to realize the connection, with the characteristics of large depth of fusion, high speed and low heat input. Common welding modes include continuous laser welding and pulsed laser welding, which are suitable for precision welding of thin plates and deep welding scenarios. Compared with arc welding, laser welds have high strength and low deformation, and are suitable for power battery packaging, stainless steel device welding and nuclear power structural components manufacturing and other fields. Especially in battery manufacturing, laser welding has become the mainstream connection method.
(1) In the automotive industry, laser welding is used to connect body panels, engine parts and other key components. For example, fiber lasers are used to weld high-strength steel parts with high precision, resulting in strong and durable joints.
(2) Electronics industryIn the electronics industry, laser welding is used to join small and delicate components with high precision. For example, diode lasers are used to weld battery cells in lithium-ion batteries to ensure the reliability of electrical connections.
(3) In the aerospace industry, the Boeing 787 Dreamliner uses a laser welding process to connect titanium alloys to composite materials, dramatically reducing the number of rivets, lowering the weight of the fuselage and improving fuel efficiency.
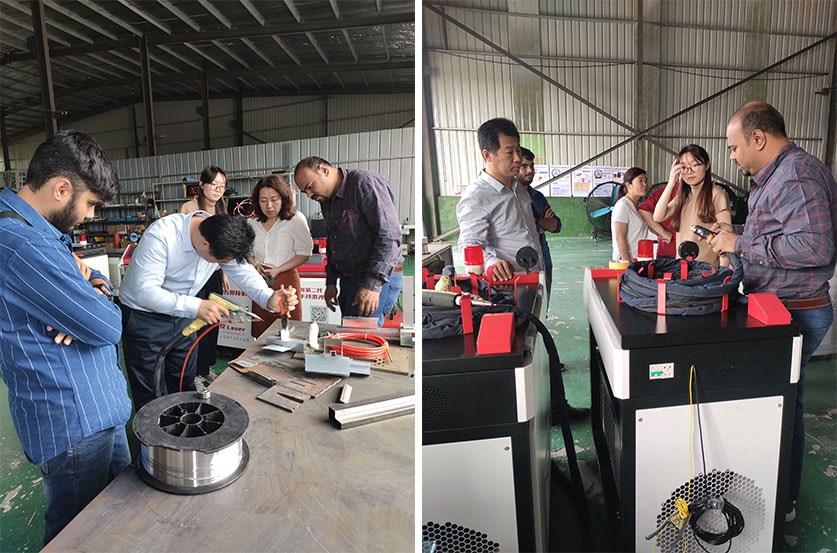
3.laser additive manufacturing
Laser Additive Manufacturing (i.e., laser 3D printing) represents a shift from “subtractive” to “additive” manufacturing by melting powders or filaments layer-by-layer to achieve a layer-by-layer buildup of complex structures. Laser-based additive manufacturing processes, such as selective laser melting and direct metal deposition, are capable of producing complex metal parts with high precision and strength. Compared with conventional processing, laser additive manufacturing can realize one-piece molding and lightweight design of complex structures while maintaining material strength.
(1) In automotive manufacturing, the titanium alloy parts of the Ferrari F1 car are manufactured using laser additive manufacturing technology, which improves the heat resistance and strength of the parts and optimizes the aerodynamic design of the car.
(2) Medical industry In the medical industry, laser-based additive manufacturing is used to produce customized implants and prosthetics.
(3) In the aerospace industry, laser-based additive manufacturing is used to produce complex components such as turbine blades and fuel nozzles.
As an important support for advanced manufacturing, laser technology is constantly expanding the boundaries of its industrial applications. At present, laser processing is also developing in the direction of higher power, higher precision and multi-process composite, such as laser-arc composite welding, laser ultra-fast micromachining, laser intelligent monitoring system and so on. In the future, with the continuous promotion of high-power semiconductor lasers, intelligent control systems and green manufacturing concepts, laser processing will continue to play a key role in intelligent manufacturing, personalized products and extreme materials processing and other fields.