Short wavelength laser welding is a highly efficient welding technique, especially for materials with high reflectivity and high thermal conductivity, such as copper and its alloys. The following are some programs and solutions for short wavelength laser welding:
- Dual-beam composite welding:
Solution: Dual-beam composite welding using infrared light and short-wavelength visible light. This method makes use of the copper near the melting point of the infrared laser absorption rate is higher, through the short wavelength laser preheating and pre-melting material, and then use the infrared laser for deep melting welding.
Advantage: This composite welding process can solve the problem of high reflectivity in single infrared laser welding, and at the same time make up for the shortage of visible laser power is not high, to realize the large melting depth welding. Studies have shown that the composite welding conditions of copper on the fiber laser absorption rate than a single light source by 20%.
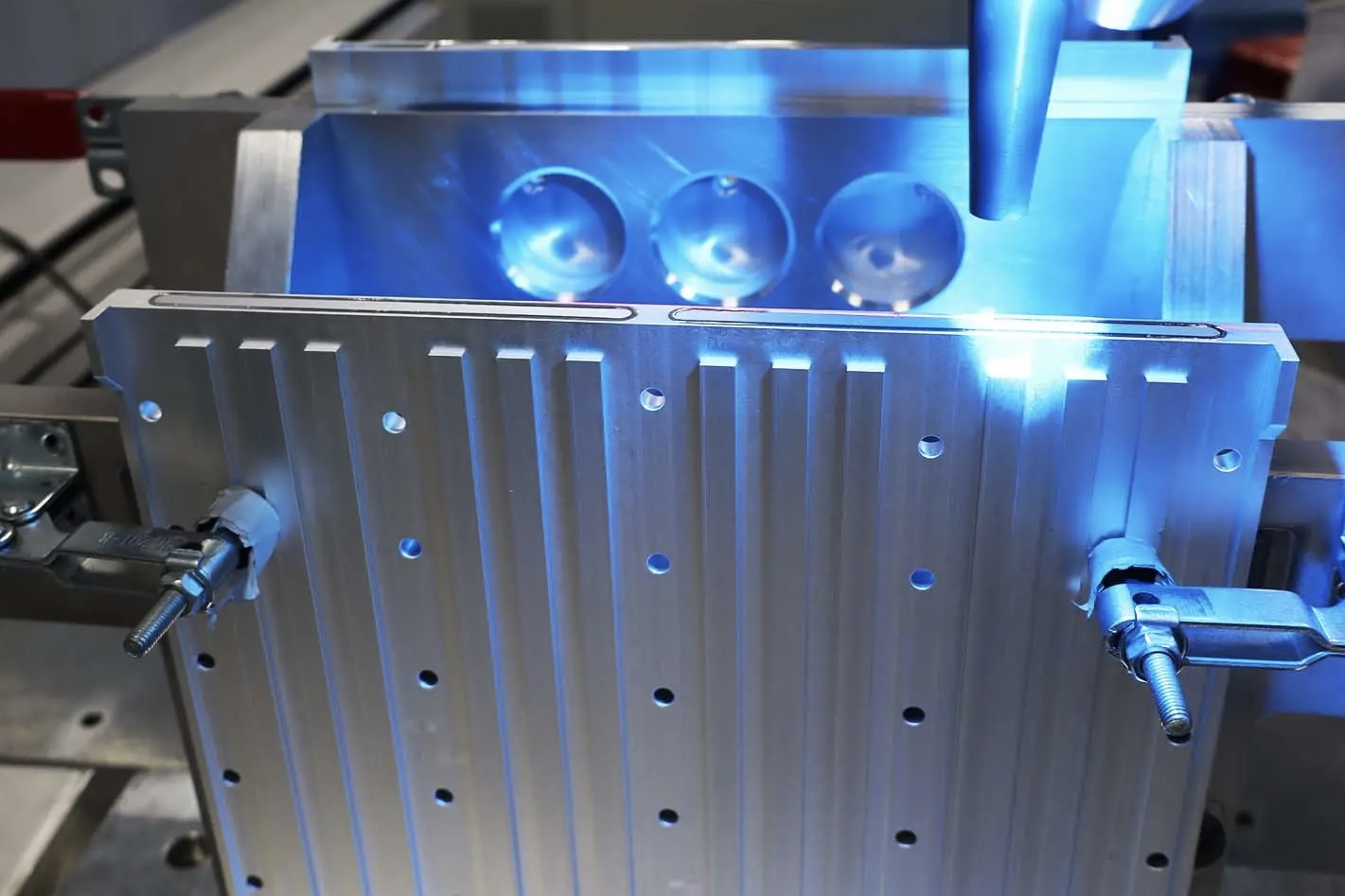
- Application of blue light laser:
Program: welding with blue light laser. Blue light laser shows high absorption rate in copper welding, which can effectively reduce spatter and improve welding quality.
Advantage: Blue light laser can significantly increase the copper absorption of infrared laser. Numerical simulations have found that the use of an additional green laser source, even with a small amount of infrared power, can help to significantly increase the infrared absorption.
- Intelligent welding head and monitoring system:
Solution: Use intelligent welding heads and monitoring systems such as the laser welding solutions offered by PRECITEC. These systems monitor the weld depth in real time during the welding process to ensure stability and consistency of the welding process.
Advantage: With intelligent monitoring systems, faulty welds can be detected at an early stage, resulting in repeatable, high-quality welds and a significant increase in production reliability.
- Welding solutions based on artificial intelligence:
Solution: Utilizing AI technology, such as the AI-based welding solution demonstrated by TRUMPF Group (TRUMPF). This solution includes AI filters and real-time welding depth monitoring technology, which can improve the recognition accuracy and depth monitoring precision during the welding process.
Advantages: AI filter through the graphic binarization process, effectively improving the recognition accuracy of the welding process, to avoid the parts surface dirt, scratches or poor lighting conditions caused by the recognition of the difficulties. visionLine OCT Check technology through the optical coherence tomography (OCT), can be high-speed high-precision depth of fusion monitoring.
- High energy density welding method:
Solution: High energy density laser welding methods such as laser deep fusion welding are used. This method generates high temperatures on the material surface by means of a high power density laser beam, which rapidly melts the material and forms the weld.
Advantage: Laser deep fusion welding has the advantages of high depth-to-width ratio, small weld width, small heat-affected zone, small deformation, fast welding speed and high weld quality.
Through these programs and solutions, short wavelength laser welding technology is able to provide higher weld quality and efficiency when dealing with high reflectivity and high thermal conductivity materials.