Laser processing is used in a large number of applications in the manufacturing of new energy vehicles, and has shown a superior price/performance ratio in many manufacturing segments due to factors such as flexibility, high processing precision, speed and good processing quality, etc. Glorious’s products have also been used in many applications in this segment, and we will introduce them today.
First of all, our products in the automotive battery and parts, interior manufacturing have shown stable and excellent processing results, such as marking and engraving, a variety of membrane airbag display cutting, surface treatment, cleaning, scribing, drilling, welding, etc., the following look at a few applications of the actual case.
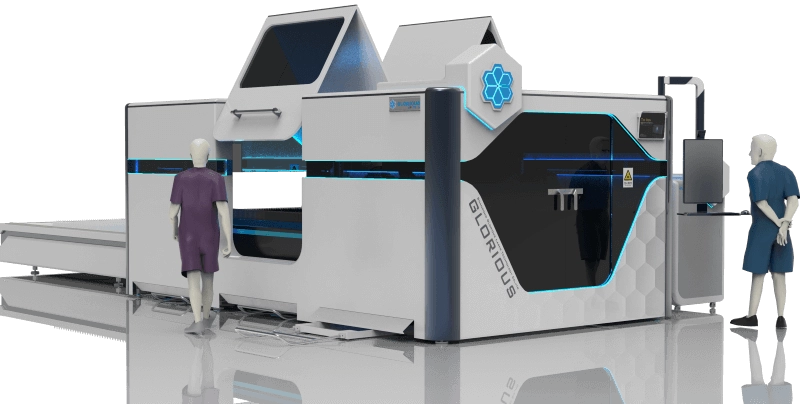
Laser Marking
Laser marking can be used on almost all materials and all kinds of irregular surfaces, and is extremely flexible, able to cope with diversified and complex needs. For automotive parts and electronic products, etc., which require high quality and durability, the high quality and durability of laser marking is an excellent choice.
Hairpin Lacquer Stripping
Organic composites such as polyamide (PA), polyether (PE) and polyimide (PI), which are commonly used as insulation materials in hairpins, absorb well at longer wavelengths within the far-infrared spectrum, so we believe that CO₂ lasers are the optimal solution for removing residues from the surface of flat copper wire. The CO₂ laser’s ability to effectively remove insulation without damaging the substrate and its cost-effectiveness make it an excellent choice for flat wire cleaning, which is now widely used.
Interior Cutting/Processing
In a variety of processes such as interior fabrics such as cutting applications, laser processing offers outstanding advantages in terms of cut quality, no burrs, no damage to the material, and superior machining and repeatability compared to conventional processes. In addition, laser processing can also be a variety of leather, fabric, synthetic materials, car trim micro-hole punching, scribing and so on.
In addition to CO₂ laser applications, our products have more and wider applications in battery manufacturing. For example, in battery manufacturing pole piece cutting, electrode three-dimensional microstructure processing, lug cutting, aluminum-plastic film cutting, welding and so on.
Metal Foil Structuring Processing
Creates 3D microstructures on metal foils through laser ablation and other treatments to enable better adhesion of active materials, thus extending battery life.
Active Material Processing
Creating diffusion pores in electrodes to optimize the electrochemical performance of the electrodes and reduce the loss of active material, Novanta’s vibrators and motors allow for the formation of fast, efficient pore patterns with micrometer-level accuracy.
Pole Piece Cutting
Laser cutting is gradually replacing mechanical slitting in the cutting process of electrode sheets. Laser pole piece cutting not only achieves high precision, but is also easy and efficient to operate, and allows changes to be made to the pattern and geometry at any time.
Laser Contact Processing
Laser Contact Processing is the process of welding multiple layers of film together to form an electrical component. Our products have a wide range of wavelength options to accommodate many types of laser sources, and the product’s oscillating technology ensures a high integrity weld.
Laser Cleaning
Removing dust, oxides or other coatings that may affect bonding quality through laser cleaning helps to improve the surface quality of the cell and enhance conductivity, among other things. Laser cleaning has become the preferred method of cleaning poles because it is green, efficient and causes little damage to the foil.
Laser Seal/PACK Welding
There are a large number of welding applications for copper, aluminum and alloy materials in single cells and battery modules that require high-quality, hermetic welding. In the final processing step, the batteries are assembled together, and for this purpose, the batteries are laser welded to the busbar, which allows flexible welding of different materials and positions.