This paper centers on the application of laser cutting technology in the processing of shaped parts to discuss the advantages of laser cutting technology to understand, clear the existence of defects in the cutting of shaped parts, and for these problems to explore specific measures to solve them, and hope to effectively enhance the application of laser cutting technology, so that the processing quality of shaped parts to ensure.
The so-called laser cutting technology, mainly through the focusing mirror in the material surface focusing CO2 laser beam to make the material melt, at the same time on the coaxial and the laser beam of compressed gas to be applied, after the melting of the material to blow away, so that the laser beam and the material in accordance with a certain trajectory for the relative movement, so as to form the cutting seam.
With the development of science and technology, laser technology has been the rapid development of the technology has a high cutting accuracy, cutting speed, not affected by the shape and the cut seam does not exist deformation, no burr characteristics, but also because of this, the technology in the field of machining has been widely used.
1 . Advantages of laser cutting technology
(1) High precision: the positioning accuracy of laser cutting technology is 0.05mm, and the accuracy can reach 0.02mm after repeated positioning.
(2) laser beam after focusing will form a very small point of light, and the power density at the intersection is very high, can quickly heat the material to the degree of vaporization, in the evaporation of the formation of holes, the beam and the material is linear relative movement, can form a continuous hole, thus forming a very small slit, usually, the width of the kerf is 0.10 ~ 0.20mm.
(3) The cutting surface is smooth: no burrs exist in the cross-section after cutting, and the roughness of the cut surface can usually be controlled within Ra12.5.
(4) has a faster speed: the cutting speed can reach 10m per minute, the maximum positioning speed can reach 70m/min, the cutting speed is much higher than the line cutting.
(5)Good cutting quality: can realize non-contact cutting, heat on the cutting edge of the impact is very small, there has not been the problem of heat deformation of the workpiece, so that the material in the punching and shearing without collapsing the edge of the phenomenon occurs, usually cut seams do not need to carry out secondary processing.
(6) The hardness of the material will not affect the use of cutting technology: the use of laser cutting technology to complete the processing of stainless steel, carbide, steel and aluminum alloy plate, regardless of the hardness of the material, can ensure that the cutting does not appear deformation problems.
(7) can effectively save investment in molds: with other types of parts processing, the use of laser processing technology does not need to apply the mold, there is no mold wear and mold repair problems, during processing to reduce the time of mold replacement, with the role of saving processing into the cost of achieving effective control of production costs, the processing of larger products have great advantages.
2. Specific measures for processing shaped parts
Combined with the material, parameters and geometric contour of the shaped material, the laser cutting technology processing procedures and process parameters for a reasonable choice, choose the appropriate processing method to effectively eliminate defects in the processing of parts, so that the quality of parts processing is guaranteed.
2.1 Interval point method
Plate parts if the length and width is relatively large, with the thickness of the workpiece and the ratio of changes in the parts will appear deformation, Figure 1 for the cutting defects schematic, for this defect, the material should be considered for the plate, the cutting method to choose. If the material of the part is carbon steel plate, and later to paint or other chemical processes, the roughness of the cut is not very high requirements, you can use the laser cutting machine itself comes with the micro-welding processing. In the processing program interface click on the relevant function button to complete the creation of micro-welded joints. If the part material belongs to the stainless steel class, the appearance of such parts are generally high requirements, if the use of micro-welding cutting, easy to produce welding melt marks, and this melt marks are not easy to be eliminated, will have a certain impact on the appearance of the parts, for this material parts, you can use the spacing point cutting method of cutting, you need to create the spacing point through the operating program. When the difference in the thickness of the material T value, it is necessary to make appropriate adjustments to the spacing, to ensure that after the completion of the cut, the two workpieces are easy to divide, and will not affect the cutting surface, after the test found that in the thickness value of T ≤ 1.5m m, the spacing value δ = 1m m, in the 2 m m ≤ T ≤ 4m m, the spacing value of δ = 0.5mm, the spacing point of the cutting method is more symmetrical in the processing of parts. applicable and can be promoted accordingly, as shown in Fig. 2.
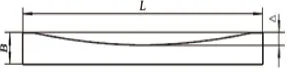
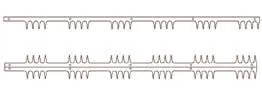
2.2 Transition lead method
Because the size of the part itself is relatively small, the cutting speed is relatively fast, and the temperature of the starting point has not been completely cooled, so it is necessary to carry out repeated cutting to complete the arc closing process, which leads to serious burn problems at the starting point and end point of the cutting, and the contour after the completion of the cutting can not reach the standard size, and the roughness of the cutting surface is seriously exceeded, and after the test, the transition method is used to merge a single part, and a single time to a number of After testing, the transition method is adopted to merge single parts and cut multiple parts at one time, and introduce the starting point and end point of cutting to the waste area of cutting to avoid the overlap of the starting point and end point of cutting, thus effectively avoiding burn defects in workpiece cutting.
2.3 Three-dimensional cutting method
Cold-formed profiled steel pipe has high strength, light weight characteristics, the use of the workpiece can make the welding process and deformation assembly problems become more simple, can save the labor required for structural installation, to achieve the performance of the products to enhance the application of the workpiece is also very wide, but due to the more varieties of the profiled steel pipe, the shape is more complex, three-dimensional geometric shape, the length of the finished product there are big However, due to the more varieties of the shaped steel pipe, the shape is more complex, three-dimensional geometry, and the length of the finished product has a great deal of difference, which leads to the workpiece in the design and processing of great difficulties.
After a long-term study of the design platform of the relevant software and PE P SPe nt a c u t three-dimensional laser cutting technology, it was found that the production of cutting fixtures positioning plate can effectively improve the efficiency and quality of workpiece positioning and cutting, and the main idea of cutting is to change the traditional spatial curved surface form of the three-dimensional workpiece cutting into a simpler two-dimensional cutting, so that the workload of the fine machining can be effectively reduced to shorten the time of manufacturing jigs and fixtures, and to reduce the time of the workpiece design. Manufacture of work fixtures and fixtures time, so that the precision of the cutting is easier to meet, and the use of three-dimensional cutting method, two-dimensional sheet material, compared with three-dimensional workpiece processing, processing is more simple and fast, can make the mounting bracket as well as the fixture production time as well as the production cost can be effectively controlled.
3. Conclusion
In summary, laser cutting technology has many advantages in parts processing, including high precision, small slit, fast speed, material saving, good cutting quality, not affected by material factors, cost savings, and is conducive to the production of new products, etc. However, there are still some defects in the use of laser cutting technology for shaped parts processing, which is mainly due to the lack of the use of laser cutting technology. Rationality, in the processing of shaped parts, we must master the parts and the characteristics of laser cutting technology, clear parts of the physical properties, shape, material, processing requirements, etc., the cutting method to make a reasonable choice, to avoid the improper use of cutting technology, resulting in parts burns, deformation, melting marks or too rough, the processing of shaped parts of the quality of the impact.