Ultra-high-power fiber lasers enable fast, high-quality cutting of thick plates, including air-assisted cutting of stainless steel, and offer many advantages over other cutting solutions.
Over the past few years, ultra-high power (UHP) fiber lasers in the 10-40kW power range have been rapidly adopted in the cutting market, and the maximum laser power for cutting applications is expected to continue to increase. This article will show the results of cutting applications in this power band and discuss the main factors driving the adoption of UHP fiber lasers: significant productivity benefits, cut quality enhancements, and the ability to cut thick plates.
Here, lasers with a power greater than 10kW are defined as UHP lasers, which enable new cutting processes and thus promote laser cutting to new markets (e.g., stainless steel thicknesses of up to 50mm can be cut using air as an auxiliary gas, and at speeds up to four times faster than high-power plasma cutting). The results show that ultra-high-power lasers are changing the way steel is cut: the use of air-assisted cutting processes instead of nitrogen and oxygen cutting processes, resulting in high-quality, high-speed and economical cutting.
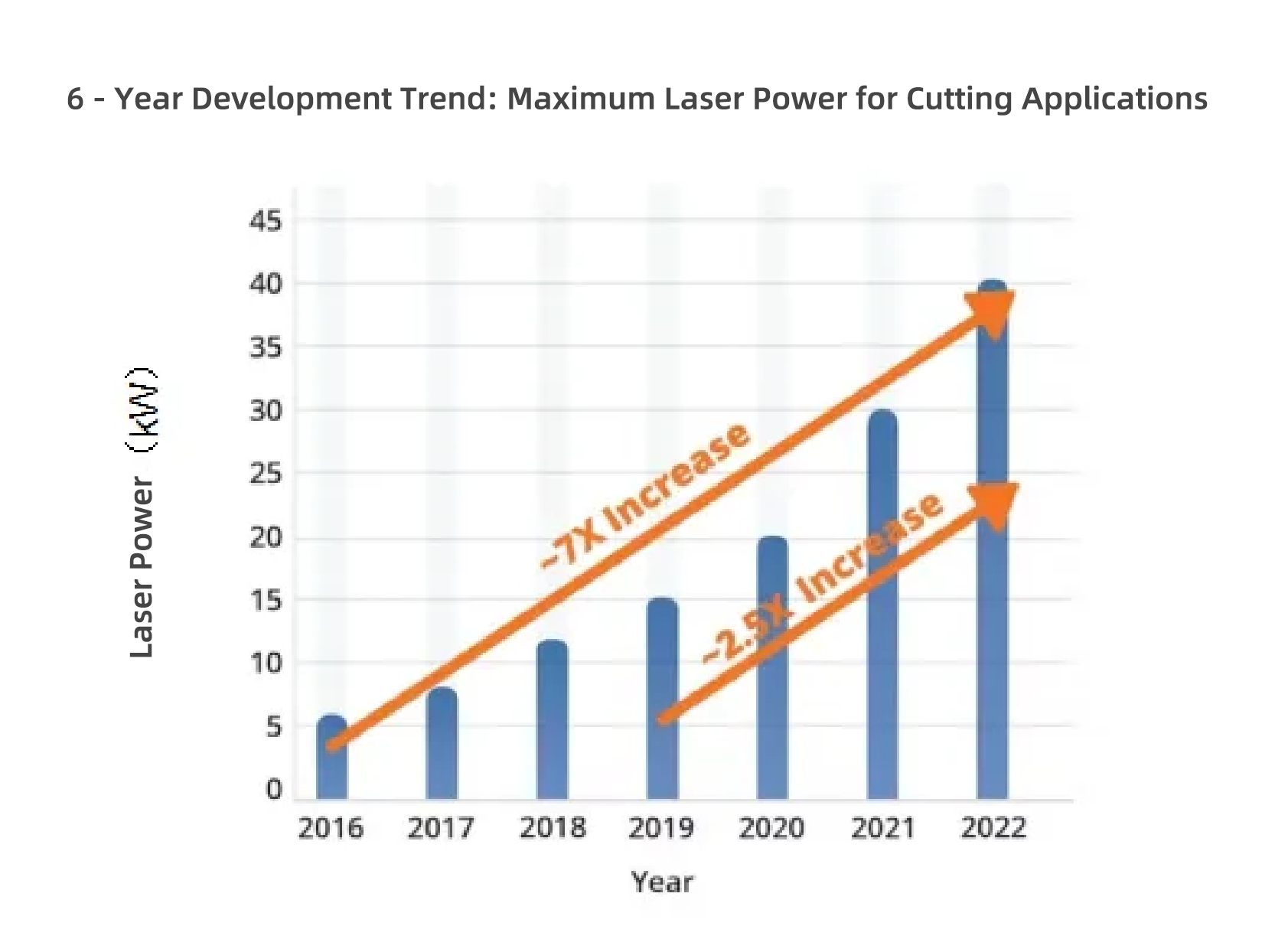
More than 50 years ago, laser cutting technology was introduced. Since then, laser cutting technology has entered a high-speed development track. 1970s, commercial laser cutting machines were introduced, and early users used them for mass production; in the 1980s, carbon dioxide (CO2) laser cutting equipment has been widely used; in the late 1990s and early 2000s, laser cutting equipment began to use high-power fiber laser; in the late 2000s, the development of kilowatt-class fiber laser cutting machines made laser cutting from small-scale applications to mainstream manufacturing processes. In the late 2000s, the development of kilowatt-class fiber laser cutting machine, so that the laser cutting from small-scale applications to become a mainstream manufacturing process. Fiber laser cutting machines have dominated the market for laser cutting of sheet metal, thanks to the ease of integration, reliability, low maintenance, relatively low investment and operating costs, high cutting yields, and the feasibility of power ramping.
In the late 1910s and early 1920s, growth in the laser cutting market came from two directions: the first direction was the low-power cutting market, which saw a surge in demand for 1~3kW cutters due to the significant cost reductions in cutting equipment; the second direction was the high-power cutting market, which was the segment of the market that drove the increasing demand for ultra-high-power lasers. Ultra-high-power lasers offer high productivity and strong technical capabilities at an affordable price, and the laser cutting sector has experienced a significant “power boost”, whereas other sheet metal fabrication processes have not seen a significant increase in the use of power over the same period of time.
The maximum laser power of the cutting machines on display at relevant fabrication exhibitions has risen from 6kW in 2015 to 40kW in 2022, a nearly sevenfold increase in power (see Figure 1)! In the last three years alone, the maximum power of laser cutting machines has risen from 15kW to 40kW, a 2.5-fold increase!
Why now is the best time?
Reliable, high-power fiber lasers were available years before the ultra-high-power cutting trend began. Industrial fiber lasers of 100 kW appeared as early as 2013. [1] But it was only in the last few years, after the price per kilowatt of lasers dropped rapidly, that the barriers to using ultra-high-power laser cutting were lowered. At the same time, laser cutting heads capable of carrying such high power in harsh cutting environments have been introduced; in addition, cutting databases for UHP cutting systems are becoming increasingly sophisticated.
Cutting Test
IPG’s 40kW YLS-40000 and IPG’s 30kW YLS-30000-ECO2 high-electro-optical conversion-efficiency fiber lasers, configured with a 100µm core diameter fiber and IPG Cut-HP cutting head, were used in this test to evaluate the cutting speeds and quality of cuts on different metals.
As far as we know, the 40kW laser power output through a 100µm core diameter fiber is the highest laser intensity currently available for industrial laser cutting. The 100µm core diameter fiber was chosen because it increases the cutting speed by 10-25% compared to a 150µm core diameter fiber.
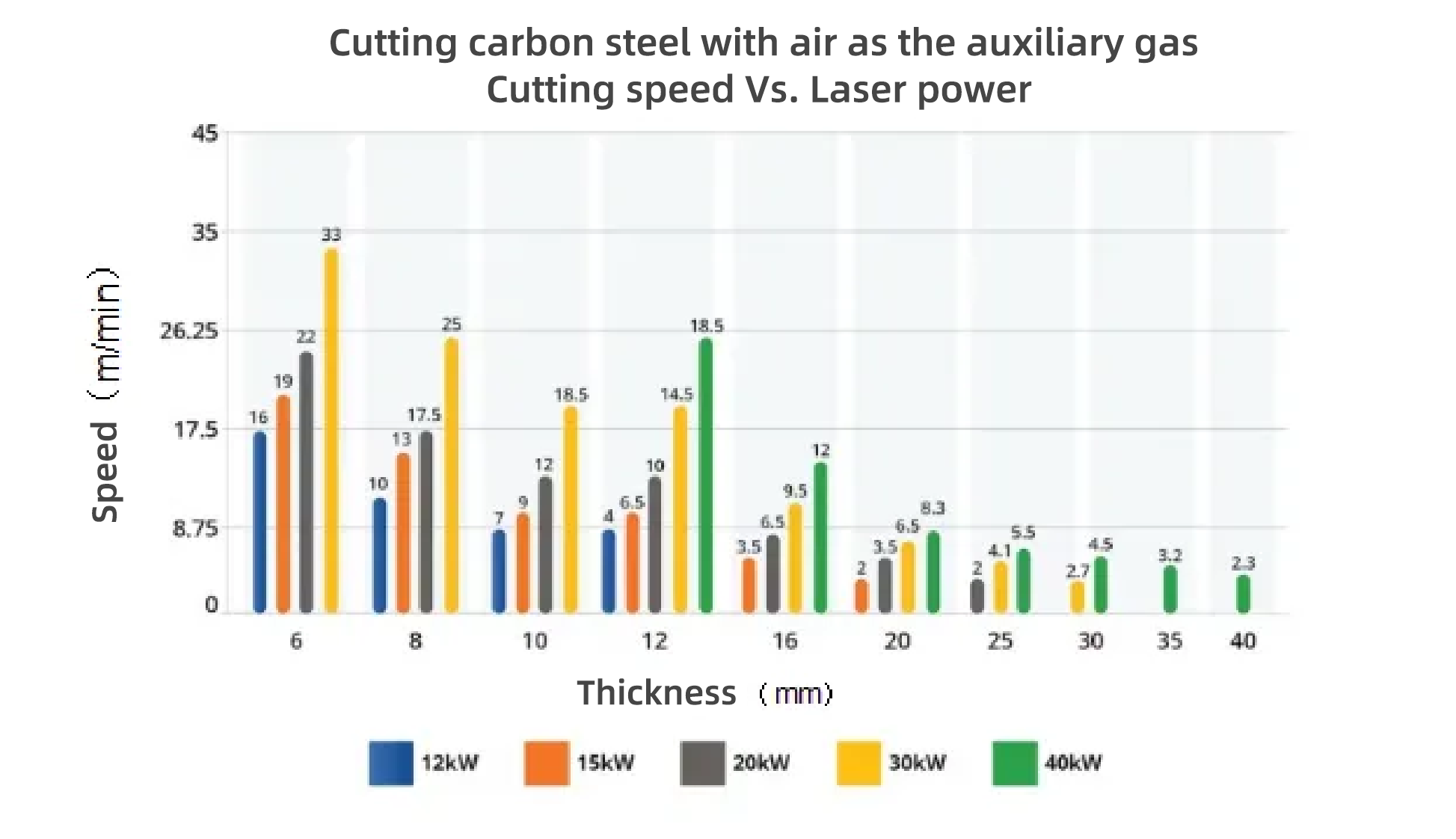
Faster cutting speeds
Experiments have shown that for all metals tested, including stainless steel, carbon steel and aluminum, laser cutting speeds increase with increasing average power (up to 40kW). Figure 2 shows the use of air as an auxiliary gas for cutting carbon steel from 6 to 40mm thick, and the graph gives the increase in cutting speed versus laser power between the 12 and 40kW power bands. For example, for cutting carbon steel of 12mm thickness, the power is increased from 15kW to 40kW, and the cutting speed is 280% of the original (a 270% increase in power); for cutting carbon steel of 20mm thickness, the power is increased from 15kW to 40kW, and the cutting speed is 420% of the original; for cutting carbon steel of 30mm thickness, the power is increased from 30kW to 40kW (a 33% increase in power), and the Cutting speed is 66% faster than the original. It can be seen that the higher power of ultra-high-power lasers will further improve the productivity of thick plate cutting.
In order to utilize the faster cutting speeds of UHP lasers to significantly reduce production cycle times, it is necessary to cut workpieces, especially thin workpieces, at high acceleration. In recent years, in order to adapt to the higher laser power, the maximum acceleration of the laser cutting machine has been changed from 1g to 3g. In the high-end market, the acceleration of the ultra-high-power laser cutting machine can reach up to 6g, and its mechanical design can ensure that the cutting trajectory will not appear obvious deviation.
Reduced Workpiece Costs and Rapid Return on Investment
Ultra-high-power laser cutting significantly reduces the cost of processing workpieces compared to low-power cutting, with a quick return on investment and higher profitability. In laser cutting applications, processing costs come primarily from gas consumption, which tends to increase significantly with part thickness.
UHP laser cutting uses the same or less gas pressure and nozzle size than low power cutting. But UHP lasers cut faster, which reduces the cutting time for individual parts and dramatically reduces gas consumption. For example, a 30kW laser can cut a stainless steel part 16mm thick in half the time compared to a 15kW laser, which reduces gas consumption by half.
The power consumption of the laser and the water cooler usually increases linearly with the laser power. Apart from that, the power consumption of the cutting machine is basically the same in all other respects. As a result, in the case mentioned earlier, the production of individual parts is half as fast, which also reduces the total cost of electricity per part by increasing the laser power. As technology continues to evolve, high power fiber lasers with electro-optical conversion efficiencies of more than 50% will help reduce electricity consumption even more. [2]
In addition to faster cutting speeds, ultra-high-power lasers can also save on gas usage. UHP lasers allow for fast, slag-free cutting of thick carbon steel with high-pressure air, compared to cutting with more expensive nitrogen or slower cutting speeds with oxygen. In both nitrogen and air cutting, UHP allows for a reduction in the air pressure required for dross-free cutting. For example, with a 15kW laser, dross-free cutting of 20mm thick carbon steel requires the use of an air pressure greater than 16 bar, whereas with 20kW or higher power, an air pressure of 10 to 12 bar is sufficient to cut the same thickness of carbon steel. Since gas usage is roughly linearly and positively correlated with pressure (at the same nozzle size), the reduction in depressurization helps to reduce gas consumption and also simplifies the requirements for gas generating equipment.
High power laser cutting equipment is twice as productive as low power laser cutting equipment, while the equipment is not twice as expensive. This is because the cost per kilowatt decreases as the laser power increases. In addition, the cost of the higher power laser is included in the total cost of the equipment at a marginal increase (compared to lower power laser equipment). As a result, UHP laser cutting machines are able to achieve twice the productivity with higher laser power, while only increasing equipment costs by 30-40%.
Due to the significant increase in productivity, UHP machines can replace multiple low power machines, with a corresponding reduction in floor space, operators, and facility preparation. On the other hand, in order to ensure productivity, ultra-high-power fiber laser cutting machines require higher reliability of the laser light source and cutting head. That is to say, for the fiber laser light source, long-term stable power output and beam quality are required, which will be affected by the quality of diodes, components and optical integration. As for the ultra-high-power cutting head, it needs to withstand high laser power, high-pressure gas, dust, process heat and high acceleration to achieve stable and reliable processing.
Table 1: Comparison of advantages and disadvantages of cutting carbon steel with oxygen, nitrogen and air
Division of a text | Oxygen | Nitrogen | High – Pressure Air |
---|---|---|---|
Gas Equipment Cost | Low | Low to High ¹ | High ² |
Gas Operating Cost | Low ³ | High ⁴ | Very Low ⁵ |
Throughput | Low | Very High | Very High |
Dross | None/Low | Medium | None/Low |
Long – Term Repeatability of Production Quality | Medium/High | Very High | Very High |
Sensitivity to Material Surface Environment ⁶ | Medium | Low | Low |
Sensitivity to Material Composition | High | Low | Low |
Heat – Affected Zone | Medium | Small | Small |
Ability to Cut Complex or High Depth – to – Width Ratio Workpieces | Medium | High | High |
Oxidation Degree of Cutting Surface | Severe | None | Moderate |
Cutting Surface Roughness (Rz) | Low | Medium | Medium/High |
Aesthetic Appearance of Cutting Surface | Good | Medium | Poor |
Kerf Width | Large | Small | Small |
Laser Power Required for Dross – Free Cutting | Low | N/A | Medium |
1 – Depends on the scale of production
2-Equipment to pressurize air and filter moisture and oil
3- Oxygen cutting uses low pressure (usually 5~20psi) and small orifice nozzles
4- Nitrogen cutting using high pressure and large nozzles
5-Air as a cutting gas source has no cost
6-Oxidation level and oxide thickness
New process for cutting stainless steel
Carbon steel can be cut with oxygen, nitrogen or air as an auxiliary gas. The advantages and disadvantages of using each of these auxiliary gases are summarized in Table 1. Although oxygen cutting excels at cutting thick carbon steel with lower laser power, it reduces productivity because cutting speed is not proportional to laser power. In contrast, with air-assisted cutting, speed is proportional to power (see Figure 2). For example, cutting carbon steel with a thickness of 16mm, with a power between 10 and 30kW, the oxygen cutting speed stays the same at about 2m/min; while with a power of 30kW, the air cutting speed is higher than 9m/min, which is 4.5 times faster than that of the oxygen cutting speed.
At lower power and lower speeds, thicknesses that could only be cut with oxygen in the past can now be cut with air-assisted ultra-high-power lasers and can be cut several times faster and with good cut quality. With low-power lasers, air cutting can result in hard-to-remove slag and poor surface quality; the new high-efficiency, ultra-high-power cutting solution offers a much better solution for industries that rely heavily on thick plate processing, such as heavy industry, and has been well received by the market.
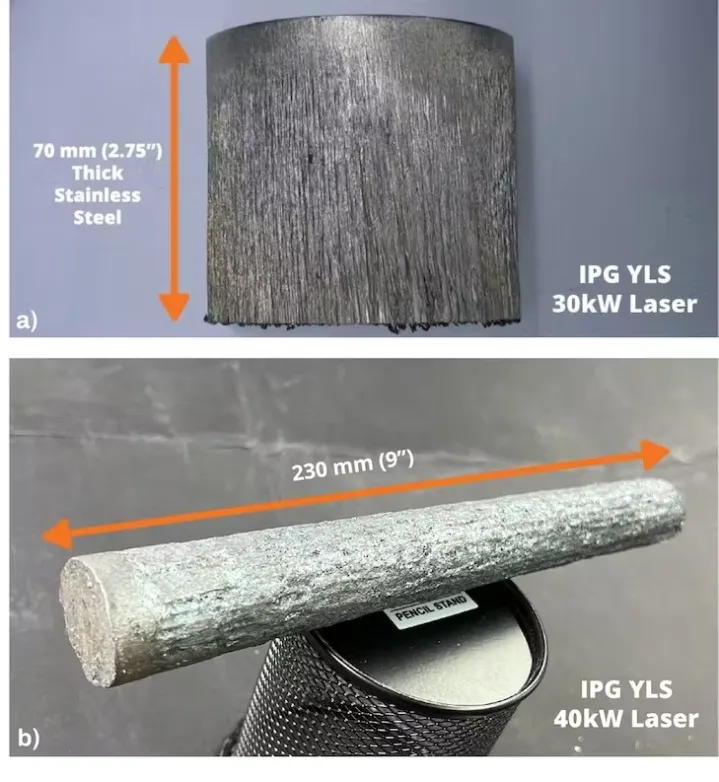
Improving thickness, throughput and quality in thick plate cutting
Tests have shown that as the power of the UHP laser increases, so does the ability to cut thickness. Cutting 70mm thick stainless steel with nitrogen at 30kW and 230mm thick carbon steel with air at 40kW, both in pulsed cutting mode, are shown in Figure 3.
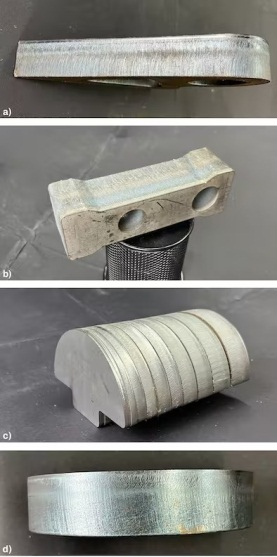
In continuous wave (CW) full speed cutting mode, carbon steel of 20mm thickness was cut with 20kW power slagless air, carbon steel of 30mm thickness was cut with 40kW power slagless air, and carbon steel of 40mm thickness was cut with 40kW power slagless air (see Fig. 2 and Fig. 4a). For cutting stainless steel, it is easier to achieve a slag-free effect, so the ultimate cutting thickness is thicker than for carbon steel (see Figures 4b and 4c).
For continuous nitrogen and air cutting, dross-free cutting and a good cutting surface can only be achieved up to a certain thickness at any given power. Above a certain thickness, pulsed cutting (slower than continuous) should be used to achieve acceptable cut quality; otherwise, the laser power must be increased. Typically, cutting speeds below 2m/min mean that there is insufficient laser power to achieve optimum cut quality in continuous mode.
For oxygen cutting of carbon steel, increasing the power will increase the ultimate thickness of the cut, provided that the “cutting surface is smooth” is satisfied; for example, the ultimate thickness of the cut is about 6~8mm for 4kW, while the ultimate thickness of the cut is 30mm for 15kW. Fig. 4d shows a sample of a 30mm-thick carbon steel piece cut with 15kW power.
Faster and cleaner perforation
By using the high peak power of the UHP laser in pulsed mode, thick metals can be perforated quickly and with minimal spattering. perforation times for 16mm thick stainless steel have been dramatically reduced from >1s for 6kW to 0.5s for 10kW and 0.1s for 20kW. In practice, perforations of ≤0.1s are generally considered to be “instantaneous”. “.
The higher peak power increases the depth-to-width ratio of the melt pool, which allows for faster joining of thicknesses with less transverse melting. The reduction in transverse melting of the material likewise minimizes top surface splashing.
The Competitiveness of Ultra-High Power Laser Cutting
Several technological developments have driven improvements in laser cutting performance over the past six years, and this technological advancement includes 1) selective focusing spot sizes through variable collimators or multi-core fibers, 2) fast beam rotation for improved cutting efficiency and cut quality on certain metals, 3) continuous lasers with high peak power for faster, cleaner perforated/complex cuts, and 4) ultra-high-power lasers.
Although the needs vary from industry to industry and all enabling technologies are used in specific areas, ultra-high power laser cutting is the leading technology trend driving improvements in laser cutting performance. This is evidenced by the large number of laser cutting machines worldwide utilizing UHP lasers. As UHP lasers become more widely known, application engineers are realizing the yield and quality advantages that UHP laser cutting machines offer.
The thickness, quality and cost-effectiveness of UHP lasers in thick plate cutting are significant, especially at 15kW and higher, where they are more competitive than high-current-intensity plasma cutters. Comparative tests show that for stainless steel up to 50mm thick, a 20kW fiber laser is 1.5-2.5 times faster than a high current intensity (300A) plasma cutter; and more than twice as fast for cutting carbon steel up to 15mm thick. Calculations show that the total cutting cost per meter is approximately twice as low with a 20kW laser compared to plasma cutting for carbon steel with a thickness of 15mm. Cutting stainless steel with a thickness of 12 to 50mm is 3-4 times faster with a 40kW laser compared to cutting with a high power plasma, and cutting mild steel with a thickness of 12 to 30mm is 3-5 times faster with a 40kW laser.
Using Ultra High Power Lasers
The main drivers for cutting with UHP lasers compared to low power lasers and other cutting processes such as plasma cutting are: higher productivity and the resulting lower cost per part cut. The speed gain from using UHP lasers brings economic benefits to manufacturers, for example, a 33% increase in power from 30kW to 40kW, but a 66% increase in cutting speed.
UHP lasers enable high-quality, fast air-assisted cutting of carbon steel, which is an advantage over oxygen cutting (which is slow) and nitrogen cutting (which is costly). In tests, air-assisted cutting of carbon steel up to 50mm thick with a 40kW air-assisted cut was 3-4 times faster than cutting with high power plasma.
Ultra-high power lasers make laser cutting more competitive in many other ways. For example, the ability to increase the thickness of cuts (cutting materials up to 230mm thick), improve cut quality, reduce or remove the cost of post-processing (the ability to minimize residue), reduce floor space and facility costs, reduce labor requirements, and improve the quality and throughput of perforations.
As UHP lasers continue to increase in power and energy efficiency, these benefits will become even more apparent: increasing their ability to quickly and economically transform cutting applications in a variety of industries.
bibliography:
1. E. A. Shcherbakov et al., “Industrial grade 100 kW power CW fiber laser,” Advanced Solid-State Lasers Congress (2013).
2. See https://bit.ly/3BwOdlS.