Laser cutting technology is an advanced manufacturing process, its most obvious advantage is the processing speed, high efficiency, can provide a better choice for the manufacturing industries. Nowadays, how to apply laser cutting technology more efficiently in the production process, is a growing concern, because it is directly related to production efficiency.
Therefore, the need for mechanical processing enterprises to increase the innovation and development of this technology, improve mechanical processing system at the same time, pay attention to the laser cutting technology, to promote a variety of mechanical products can be comprehensively enhance the level of manufacturing. In this paper, we will analyze and discuss the application of laser cutting technology in machining, aiming to provide scientific references for people in the same industry.
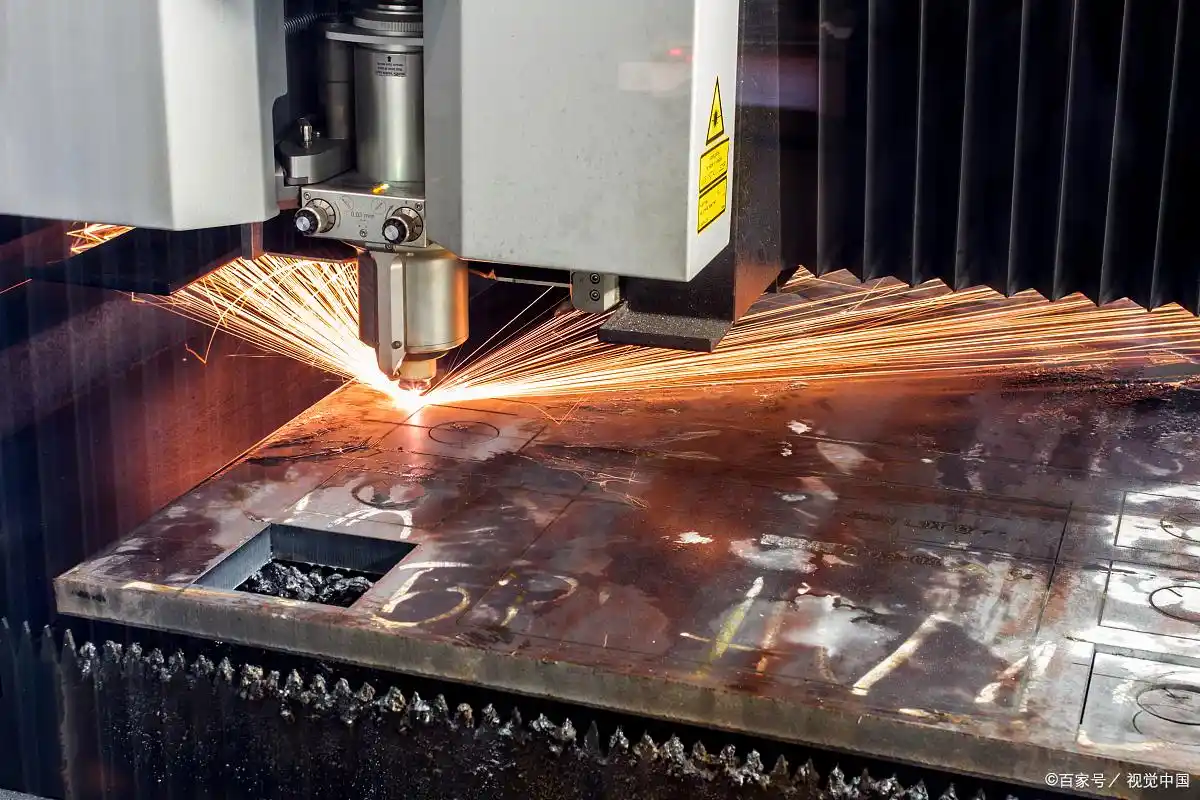
Laser cutting technology is used in the machining industry on the principle of using an auxiliary gas to melt or vaporize a workpiece by focusing a high-energy-density laser beam on its surface using laser cutting technology. Although laser cutting technology is now widely used, it is still relatively advanced overall, thanks to the uniqueness of its processing method. In today’s machining operations, laser cutting technology has developed into a widely adopted and technologically mature and complete processing method, and its application is becoming more and more common and in-depth. All major machinery manufacturing-related enterprises need to apply laser cutting technology more effectively to enhance the quality of their own mechanical parts processing and processing efficiency, in order to improve their competitive advantage in the market!
Advantages of laser cutting
1. High cutting precision and narrow kerf
Laser cutting technology is an advanced processing method that skillfully utilizes monochromatic and highly coherent laser beams, focuses these beams on a very small area, and realizes efficient, high-quality cutting of materials through precision laser cutting equipment. It is precisely because of these focused laser beams, coupled with precision equipment, that the laser cutting process has a higher degree of accuracy. Typical laser cutting equipment has an accuracy of 0.5mm and repeatability of 0.02mm, and the accuracy of top-of-the-line laser cutting equipment has become even higher as the laser cutting process has been optimized. The accuracy of laser cutting equipment is also due to the focus of a small area of the laser beam, the laser beam of the concentration of the convergence of the formation of a very fine point of light, when the energy density of this point of light accumulates to a certain threshold, will trigger the focusing area of the material of the rapid heating until vaporization or melting, and then the material vapors quickly escaped, so as to form a clear and precise hole in the material, when these laser beams are moved, laser beams When these laser beams are moved, the energy density of the laser beams is rapidly released, and a few fine holes are connected into a rather narrow crossover.
2. Smooth cutting surface and high speed
Laser cutting technology is known for its excellent cutting effect, the cutting surface is relatively smooth, the maturity of this process is also relatively high, after cutting the surface of the material is basically clean and burr-free, roughness is not as good as the specialized finishing, but also be able to control within Ra12.5. Compared with traditional processing methods, such as plasma processing or manual operation, laser cutting technology shows obvious advantages. As mentioned above, it can accurately control the shape and size deviation of the processed parts, i.e., high precision, which also ensures the consistency and neatness of the section of the parts after laser processing.
This feature greatly simplifies the subsequent splicing, assembly and other processes, optimizing the entire processing process, eliminating the tedious grinding steps, thereby comprehensively improving the overall quality of the product. Concentrated beam of light in the laser cutting heating speed, the workpiece can be melted or vaporized in a short period of time, its cutting speed can be increased accordingly, its cutting speed can easily reach 10m/min, positioning speed of up to 70m/min, in the process of operation, the speed of the obvious advantages. This speed performance is far beyond the traditional linear cutting method, fully demonstrating the huge advantages of laser cutting in speed.
Laser cutting technology for machining applications
As an advanced processing means, laser cutting technology is widely used in the processing of various materials, including titanium alloy, steel, aluminum alloy and other metal materials, as well as glass, plastic, ceramics and other non-metallic materials, showing its wide adaptability and flexibility. The most significant feature of this technology is its non-contact processing mode, effectively avoiding the deformation of the workpiece caused by direct contact in traditional machining.
1. Laser cutting technology in metal workpiece processing
In the field of metal processing, especially in the modern machinery manufacturing industry, laser cutting technology has become an indispensable technical means. The advantages of laser cutting lies in its high precision, high efficiency and adaptability to a variety of different materials, which makes it in the field of metal processing application cases are diverse, involving a very wide range of applications. Take the automobile manufacturing industry as an important application field — laser cutting technology.
A large number of metal parts, such as the body, doors, roof, engine parts, etc., the traditional mechanical processing methods are not only time-consuming, high cost, but also may cause greater damage to the material. The application of laser cutting technology can not only improve processing efficiency, reduce production costs, but also ensure the accuracy and quality of the workpiece. Laser cutting can play a role in the processing of small screw holes to large areas of sheet metal parts, to achieve a variety of specifications and precision requirements. Another example, stainless steel and other materials processing is also a typical application of laser cutting technology .
Stainless steel is good corrosion resistance, beautiful and generous, in construction, automotive, home appliances and many other fields have a wide range of applications. Laser cutting can effectively process different thicknesses of stainless steel materials, and the quality of the cutting surface is high, and the quality of the kerf can even be comparable to traditional mechanical cutting. Other high-tech areas of laser cutting technology, such as aerospace, electronic information, aerospace, etc., China is currently more widely used laser cutting technology.
For example, many structural parts of the aircraft and key components need to be processed by laser cutting. These high precision materials and structures that require extremely high processing accuracy and quality, due to the high precision characteristics of laser cutting, it is difficult to meet the needs of traditional processing methods, and laser cutting is perfectly adapted to the needs in this regard.
2. Laser cutting technology applied to the processing of non-metallic materials
Non-metallic materials, such as various plastics, glass, ceramics, etc., because of its high absorption rate of laser, laser cutting technology has become an ideal choice for processing these materials. First of all, non-metallic materials can be laser cut faster because they have a higher laser absorption rate than metals, which means that the laser can heat and vaporize the material faster.
For example, when making templates or cutting precision parts such as complex jeweled bearing holes, laser cutting can complete complex cutting jobs efficiently, greatly reducing production cycles. Secondly, non-metallic materials usually have a lower thermal conductivity than metals, which means that the laser beam is more likely to focus its energy and less likely to cause side effects such as heat-affected zones. As a result, lasers can achieve high quality cuts in non-metallic materials, and the cuts are usually very clean and do not require subsequent processing. In specific application cases, such as the machining of holes for jewel bearings in watches, lasers can accurately cut high-precision holes for mounting jewels and keeping them in place. Laser cutting can also be used to quickly and accurately cut the required parts when creating prototype materials for 3D printed models.
3. mechanical mold manufacturing laser cutting technology
The application of laser cutting technology in the field of machinery and mold manufacturing is undoubtedly a great innovation for the modern manufacturing industry. It is with its high precision, high efficiency, non-contact processing and a wide range of material adaptability and other advantages, completely changed the traditional mold manufacturing process. In the mechanical mold manufacturing, laser cutting machine can accurately according to the design drawings, metal, non-metal and other materials for rapid, detailed cutting. Whether it is complex geometric shapes, or fine contour lines, laser cutting can easily cope with, to ensure the accuracy and consistency of the mold. This high-precision cutting capability not only improves the manufacturing quality of the molds, but also greatly shortens the production cycle and reduces the manufacturing cost.
In addition, the non-contact processing characteristics of laser cutting to avoid the tool wear, cutting force and other factors lead to mold deformation or damage in the traditional machining process. This not only protects the integrity of the mold material, but also extends the life of the mold, the scrap rate is reduced. For the need to respond quickly to market changes, frequent replacement of mold manufacturing enterprises, laser cutting technology is to provide great convenience. Can be in a short period of time, to help enterprises quickly launch new products, in the mold cutting production to seize the market opportunity.