In modern industrial production, the application of laser technology is becoming increasingly widespread, from fine marking to deep engraving, and even complex cutting processes. Choosing the right laser wavelength and power is crucial. Different materials have varying absorption characteristics for lasers, so understanding these properties and selecting appropriate laser parameters based on specific needs is key to ensuring processing results.
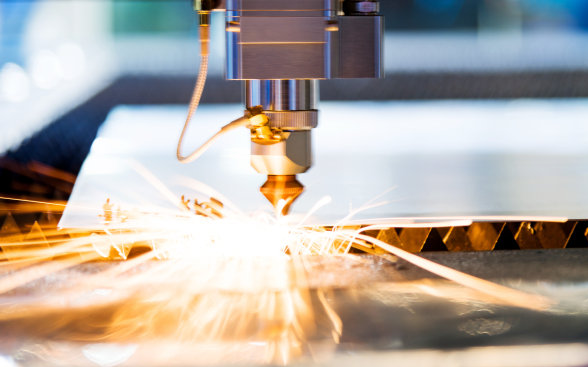
How to choose the right laser wavelength?
Wavelength selection: material absorption properties are prioritized
- Common metals (iron, aluminum, stainless steel), rare metals and alloys (titanium, copper), metal oxides, etc.
Recommended wavelength: 1064nm infrared light. Reason: Metal has high absorption rate of infrared light, suitable for deep engraving and welding.
Recommended wavelength: 355nm ultraviolet light. Reason: suitable for high-precision marking, especially for heat-sensitive metals (such as thin copper sheet) is better, to avoid thermal deformation.
- Non-metallic materials, plastics (ABS, PC, epoxy resin), rubber, acrylic, glass, ceramics, crystal jade, bamboo and wood products, paper, leather, fabric and so on.
Recommended wavelength: 532nm green light. Reason: Applicable to glass, ceramics, crystal and other brittle materials with higher absorption rate.
Recommended wavelength: 355nm ultraviolet light. Reason: Cold processing characteristics reduce thermal damage, suitable for fine marking (e.g. electronic components, translucent keys).
Note: Medical/Food Packaging: UV laser for non-polluting marking (e.g. pharmaceutical packaging, food bags).
How to choose the right laser power?
Power Matching: Machining Objectives Determine Intensity
Processing type | power range | Applicable Scenarios | Reference Case |
Fine marking | 3W–10W | Electronic components, film marking, shallow engraving | UV laser marker chip (power 5W) |
Universal engraving | 10W–30W | Metal nameplate, plastic case, bamboo and wood | 20W laser engraved stainless steel |
Deep engraving/cutting | 30W–60W+ | Thick metal cutting, carbide machining | 50W Cutting 3mm Aluminum Plate |
Ultra-high precision machining | Picosecond laser | Sapphire dicing, wafer micromachining (ultra-short pulse width required) | Picosecond laser processing of OLED panels |
In conclusion, choosing the right laser wavelength and power requires considering factors such as material type, processing goals, and required precision. By properly matching laser parameters, not only can processing efficiency be improved, but product quality can also be ensured, meeting the needs of different industries. We hope this article provides you with valuable insights and helps you achieve success in the field of laser processing.