Fiber laser cutting machine has many advantages, such as high cutting accuracy, narrow slit, smooth cutting surface, high efficiency and so on. At the same time, the use of fiber laser cutting machine in the safety and environmental protection is a significant advantage. In the future development trend, fiber laser cutting machine will occupy the position of mainstream equipment.
But do you have questions about why the cutting efficiency is still not good? Why the cutting effect is not good? Why the cost remains high?
1.Cutting speed
Cutting speed is one of the advantages of laser cutting, but the cutting speed is not the faster the better, in the case of a certain laser power, you need to choose the appropriate cutting speed according to the cutting plate, in order to make the cutting surface beautiful grain, to obtain high-quality cutting workpiece, can be used in the following ways to determine the appropriateness of the cutting speed, and then adjust the cutting speed:
- Observe the cutting spark
When the cutting speed is appropriate, the cutting sparks are spread more evenly from top to bottom; when the cutting speed is too fast, the cutting sparks will be tilted; when the cutting speed is too slow, the cutting sparks are gathered together, not spread and less. - Observe the cut sheet
When the cutting speed is appropriate, the cut surface shows a smooth line, and no slag in the lower half. Cutting speed is too fast, may not be able to cut through, sparks spraying; some areas can cut through, some areas can not cut through; cutting section is oblique lines, the lower part of the slag. When the cutting speed is too slow, it causes over-melting, the cut section is rough, and the slit becomes wider.
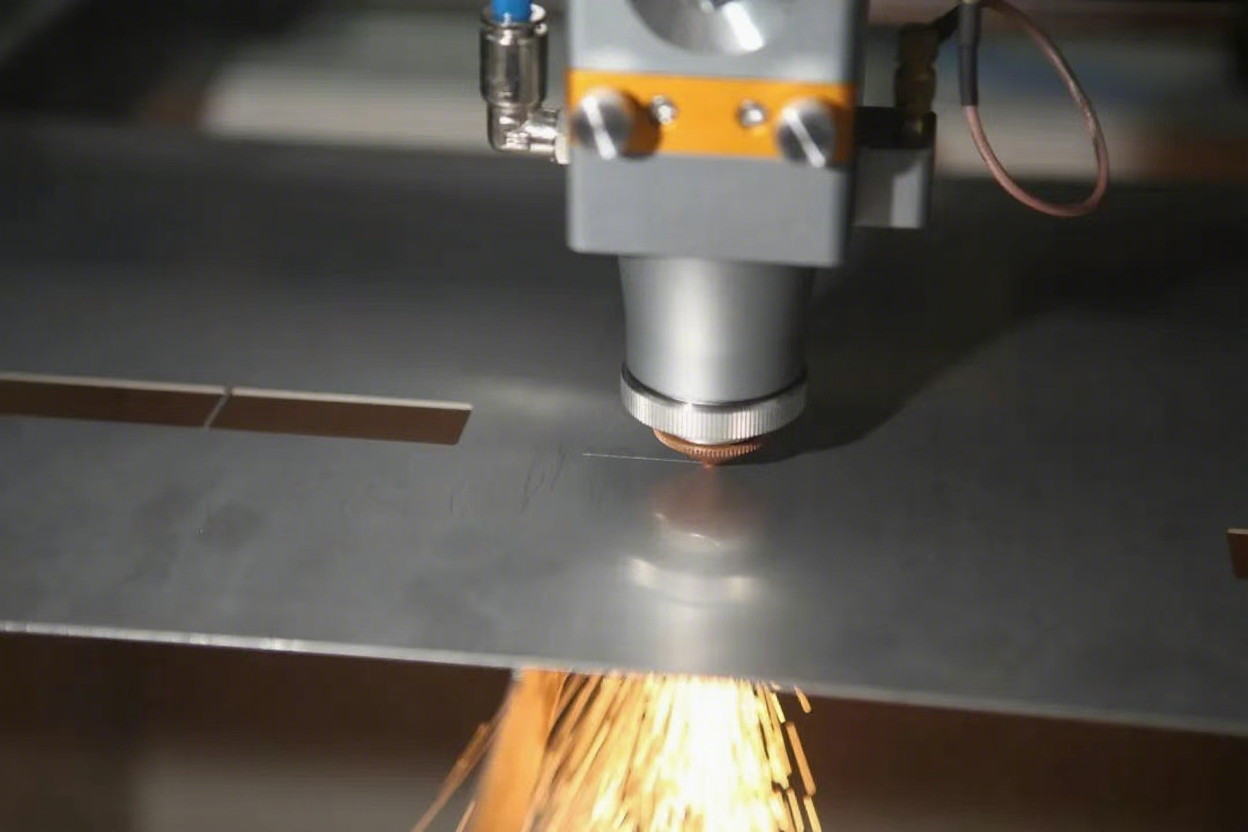
2.Nozzle and nozzle height
Nozzle as a beam and auxiliary gas channel, nozzle shape, aperture and nozzle height will affect the cutting effect.
Nozzle is mainly to control the gas diffusion area and size, thereby controlling the quality of cutting; to prevent slag and other debris upward rebound, through the nozzle, contamination of the lens. Generally speaking, the cutting of thin plates from the focus of the small amount of choice of small-diameter nozzles; and cutting thick plates required to cut a large slit, a large spot, the choice of large-diameter nozzles.
Nozzle is divided into single-layer and double-layer, single-layer laser nozzle for melting cutting, that is, the use of nitrogen as an auxiliary gas, cutting stainless steel and aluminum, etc.; double-layer laser nozzle is generally used for oxidative cutting, that is, the use of oxygen as an auxiliary gas, used for cutting carbon steel.
The height of the nozzle is the distance between the nozzle outlet and the surface of the workpiece. When cutting, this height is usually set at 0.3mm-0.8mm, too low will cause the nozzle to collide with the surface of the workpiece easily, too high will reduce the concentration and pressure of the auxiliary gas, resulting in a decline in cutting quality. When piercing, the height of the nozzle can be raised appropriately to prevent the slag generated from backfiring on the lens.
3.Focus position
After checking the actual zero focus of cutting through the previous article, in the actual cutting process, we need to set the appropriate focus position in order to get a better cut surface effect of the cut workpiece:
- Zero Focus
The focal point is on the surface of the workpiece, suitable for cutting thin plates. - Negative focal length
The focal point is under the surface of the workpiece, usually at 1/2-2/3 of the thickness of the workpiece, so the range of the smooth surface is larger and the cutting seam will be wider than that of zero focal length. - Positive Focal Length
The focal point is on the upper surface of the workpiece, generally applicable to the cutting of thick carbon steel (thick plate requires a larger slit, while a negative focal point will lead to carbon steel overburning).
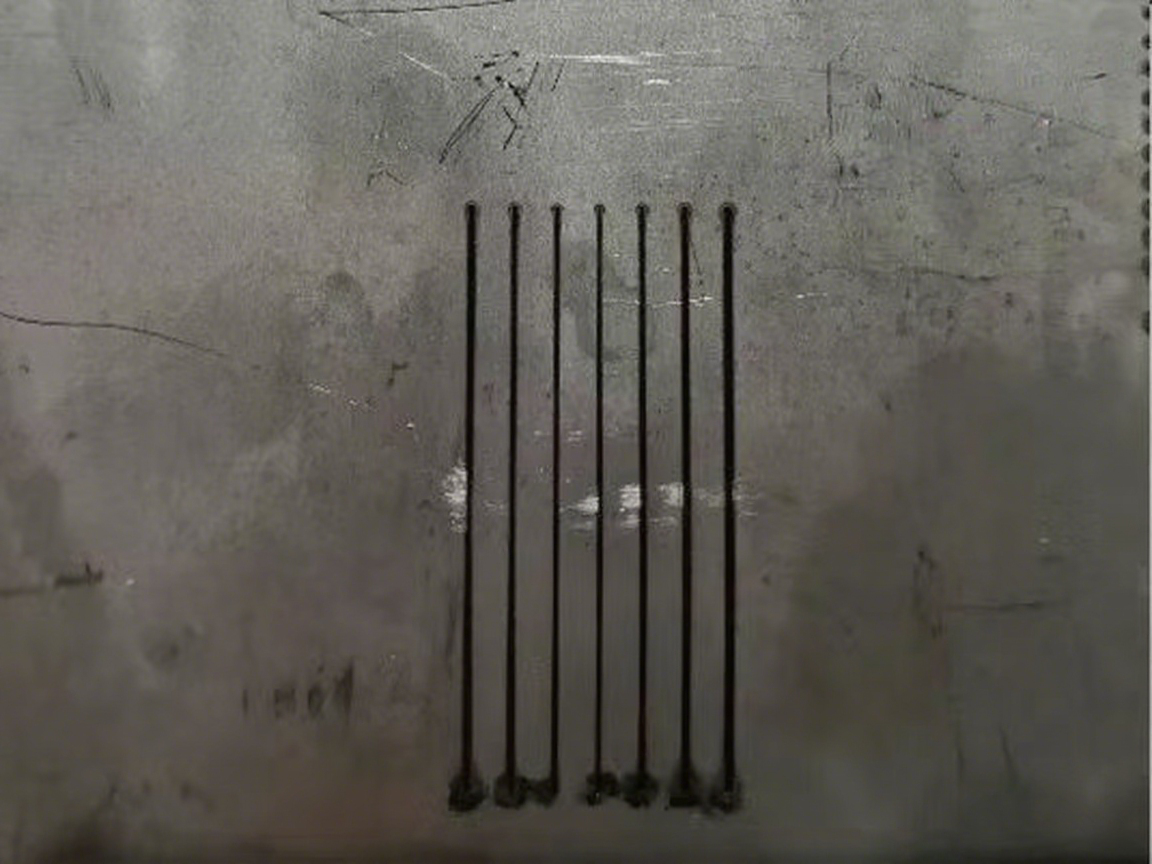
4.Protective gas pressure
The size of the auxiliary gas pressure on the fiber laser cutting machine cutting effect also has an impact on the air pressure adjustment, can also improve the cutting effect:
- Insufficient gas pressure
Insufficient gas pressure can not remove the slag generated by cutting, not easy to penetrate, resulting in slag on the cutting surface; cutting speed can not be increased, affecting the efficiency of cutting. In general, high-speed cutting of thin plates require higher gas pressure to prevent the slag attached to the back of the cut seam; and when the material is thicker or slower cutting speed, the gas pressure can be appropriately reduced. - Excessive gas pressure
Increase the gas pressure to a certain extent can improve the cutting speed, but too much gas pressure will make the cutting speed is reduced. It is because under high pressure, the gas flow rate is too fast will enhance the cooling effect, and even interfere with the focusing of the beam energy, resulting in a decline in cutting quality and efficiency. At the same time, too high a gas pressure will lead to thicker cutting surfaces and wider slits.
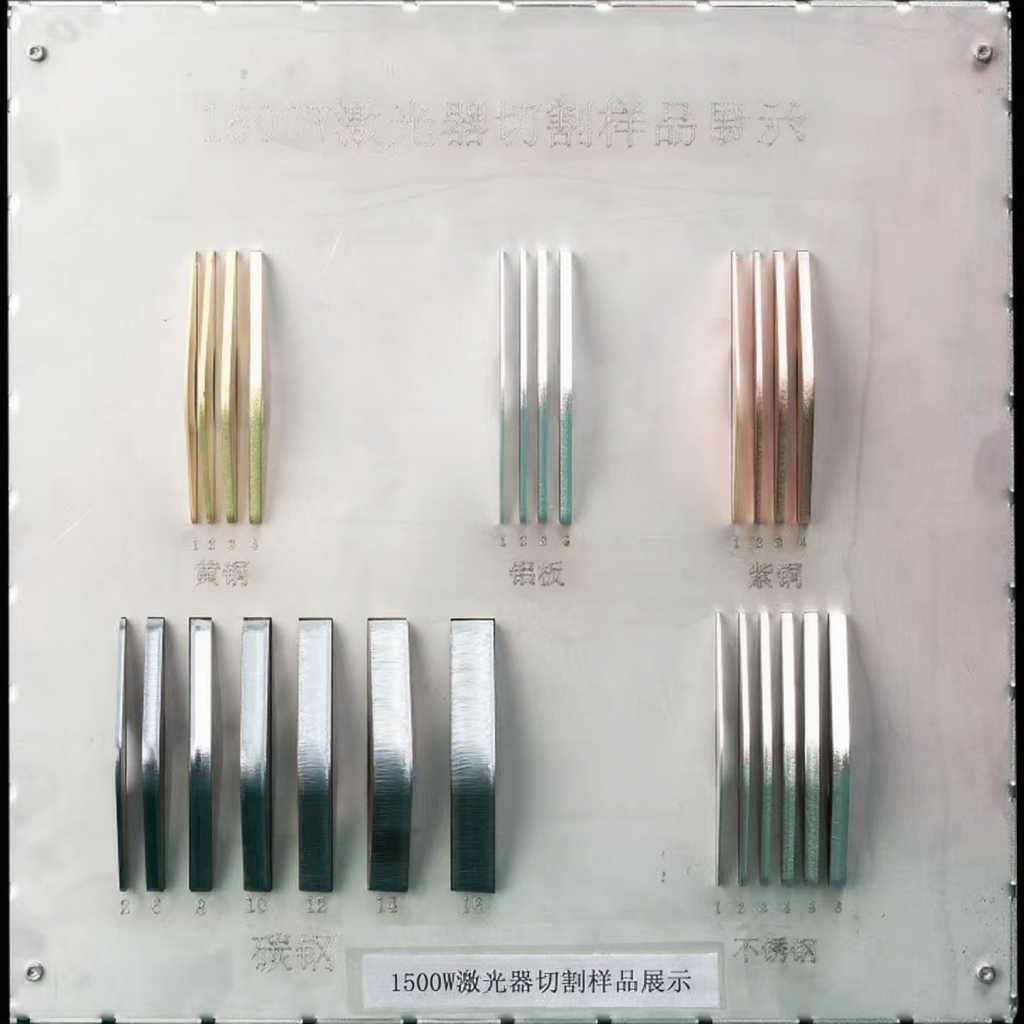
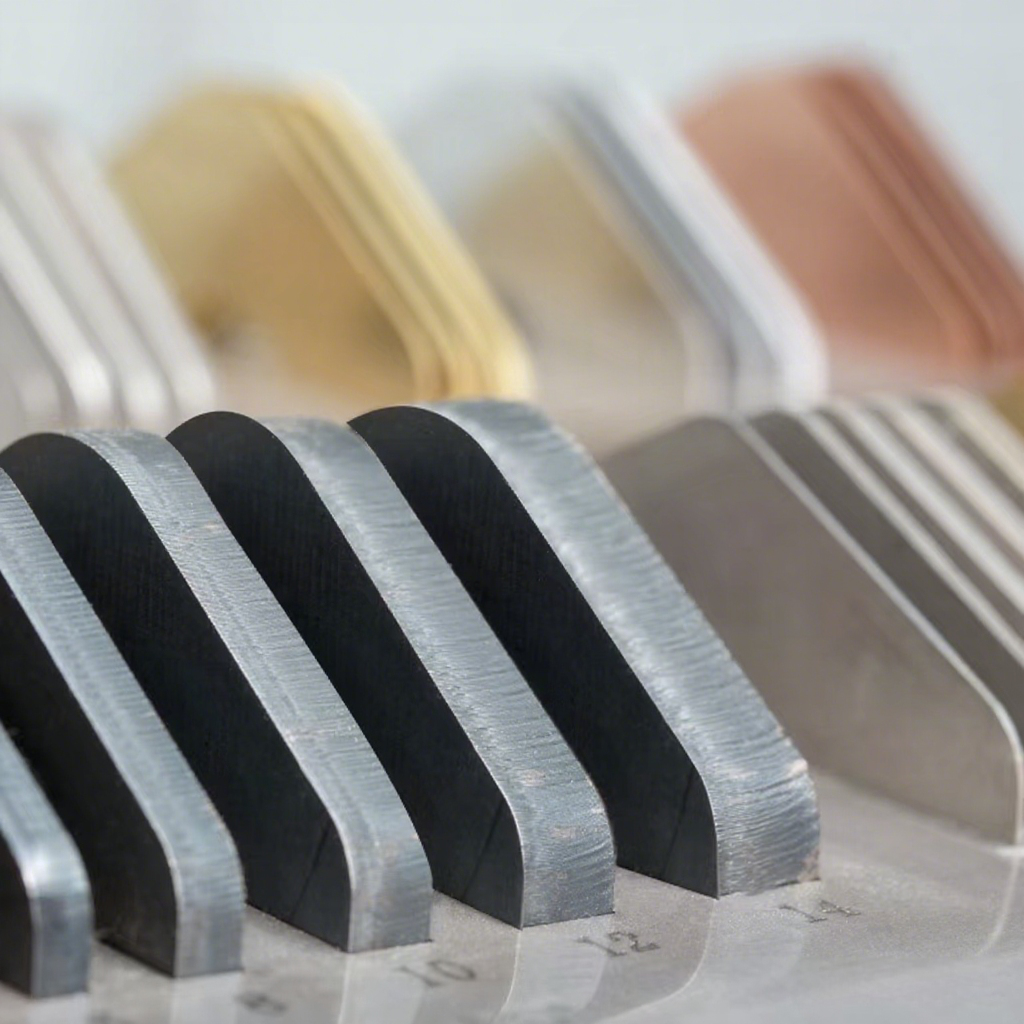
1500W Plate Cutting
summarize
Selected the excellent cutting equipment, do a good job of pre-cutting checks. Laser cutting process parameters, it must be adjusted according to the actual situation when cutting, in specific applications need to be based on the situation and choose the most appropriate cutting parameters. In the production of each of our cutting process optimization is also an important means of maintaining long-term stability and leadership.