With the development of industrial technology, laser cutting has become an indispensable part of modern manufacturing. Among various laser cutting technologies, fiber lasers and CO2 lasers are the two most common types. Each type of laser has its unique advantages and suitable applications. Understanding the differences between them is crucial for selecting the best processing solution for your needs. This article will provide a detailed comparison of the characteristics, advantages, disadvantages, and application scenarios of these two laser cutting processes to help you make an informed decision.
Fiber Lasers
Simply put, the principle of a fiber laser is to generate a laser beam through a diode, and then use a fiber optic cable, which is similar to data transmission, as a medium to guide and amplify the light energy. The amplified laser beam is collimated or straightened on the fiber optic cable and finally focused on the material to be cut through an optical lens.
Compared with the traditional CO2, the electro-optical conversion efficiency of the fiber laser is twice as high as the original; the transmission is realized through fiber optic cables, which does not need to be equipped with expensive optical lenses. Moreover, unlike traditional CO2 lasers, the cutting head comes with its own focusing lens directly, which does not require the user to configure additional consumables.
The advantages of fiber lasers are mainly:
- Unlike traditional CO2 resonant cavities or disk lasers, fiber lasers require no moving parts or lens assemblies during the generation of the laser beam, resulting in reduced maintenance requirements and lower operating costs.
- The electro-optical conversion efficiency is dramatically improved, significantly reducing operating costs. A 3 kW fiber laser consumes only one-third the power of a CO2 laser with an average output of 4 kW.
- Higher speeds in cutting thinner sheets. Fiber lasers are up to three times faster than 4 kW CO2 lasers for straight line cutting of soft steel, galvanized steel or stainless steel up to 1 mm thick. It is also twice as fast when the thickness is increased to 2 millimeters. 4.
- Highly reflective materials can be cut without fear of back reflection damaging the machine. This allows the fiber laser to be used to cut copper, brass and aluminum.
- 50% longer maintenance intervals and 50% lower maintenance costs.
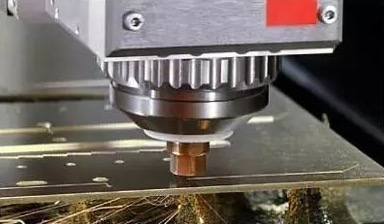
CO2 Laser
Compared to the CO2 laser cutting process, the fiber laser process suffers mainly from poor speed when cutting thickened materials with a thickness of more than 5 mm, whereas the CO2 cutter is not only faster when cutting in a straight line, but also requires much less time for punching the holes at the beginning of the cutting phase. In addition, the CO2 process has the advantage of a flatter seam surface when cutting thickened materials.
- More than 70% of those purchasing fiber lasers are subcontractors, and only a small percentage of the remainder are OEMs. This is surprising because the advantages and disadvantages of fiber lasers are very clear and depend largely on the material to be processed, so we would normally expect that OEMs would prefer fiber lasers. For subcontractors, on the other hand, they can’t anticipate what the next job is going to be and the thickness of the material that needs to be processed, so theoretically, CO2 lasers have a wider range of applicability and should be more advantageous.
- only 31% of subcontractors use fiber lasers as a single laser, the remaining 69% are equipped with multiple lasers so that the user can choose the right machine for their needs.
- The main reason why users decide to purchase fiber lasers is the faster cutting speed when cutting thinner sheets (1 to 2 mm thick, not more than 3 mm).
- Another important reason for choosing the fiber laser process is the low running cost and low power consumption. This is particularly important for factories where electricity consumption remains high.
Conclusion: Fiber Laser Process vs. CO2 Laser Process
According to Bystronic’s current statistics, the majority of users who prefer the new fiber laser are subcontractors, either companies that specialize in cutting thin sheet metal, such as sheet metal parts for retail terminals or white goods, or companies that are already equipped with CO2 lasers and wish to expand their existing sheet metal cutting capabilities by adding a fiber laser.