Laser welding has become a recognized technology for joining materials ranging from delicate plastics to dense metals. Applications include medical, aerospace, military, alternative energy and many other high-profile industries. Laser welding is used for everything from sealing microelectronic devices implanted in the human body to joining parts of rocket fuel tanks.
One of the central decisions that needs to be made is whether to use a continuous wave laser or a pulsed laser for the welding process.
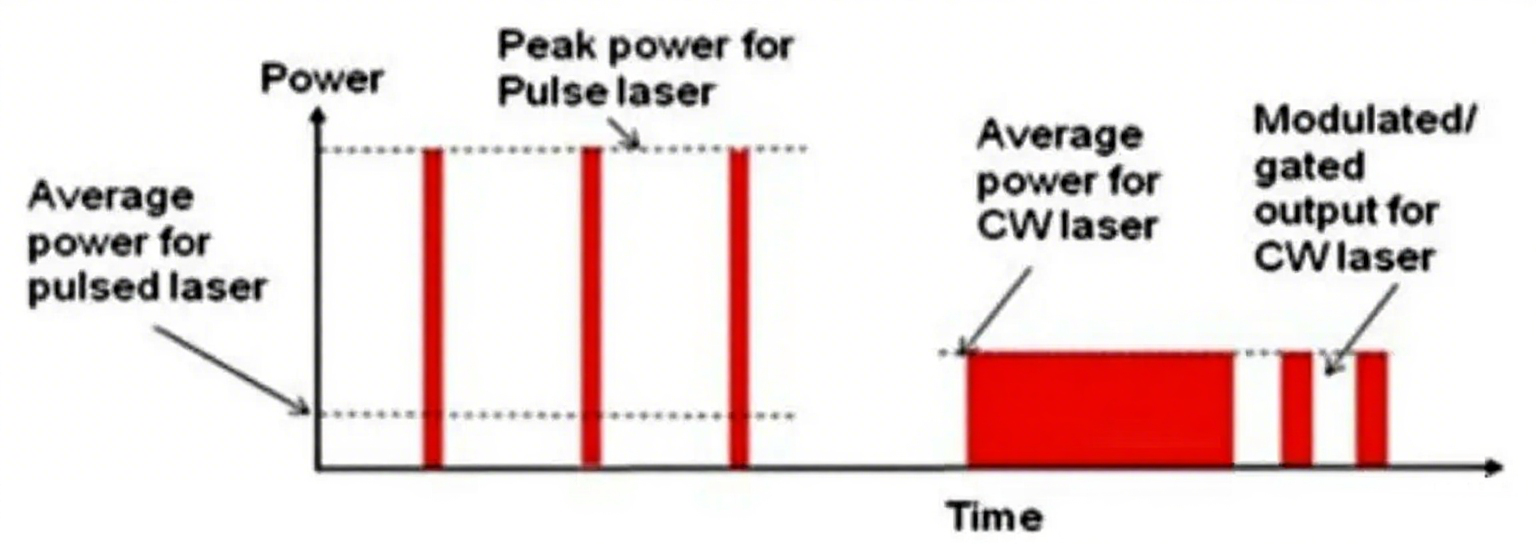
Continuous Wave Laser Welding
Continuous wave (CW) lasers are lasers that emit a constant, uninterrupted beam. They are typically fiber lasers that use an open diode to excite the gain medium to output the laser light.CW lasers are particularly well suited for deep fusion welding (depths greater than 0.060 inches) and for welding crack-prone materials such as high-carbon stainless steel.
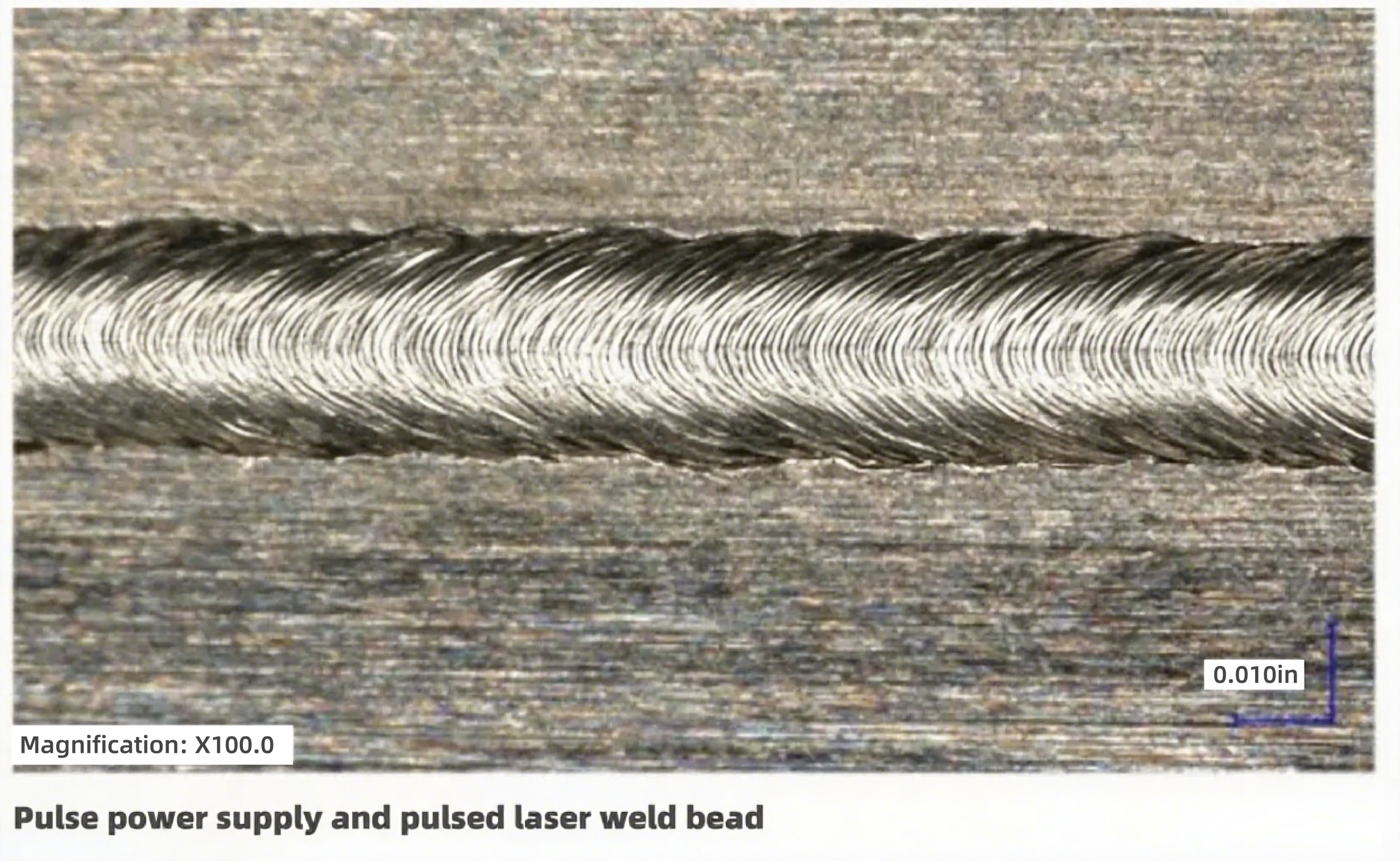
Continuous wave lasers range from as low as 200 watts to over 100,000 watts. Continuous wave laser welding requires 200 watts or more to successfully join most metals. This wide power range, combined with the high energy density, helps to fuse metals with different thermal and reflective properties. For example, ferrous metals such as stainless steel can be joined at lower power (about 200 watts), while materials such as aluminum and copper require higher power (600-800 watts) to join.
Continuous wave lasers typically operate at higher feed rates to prevent parts from overheating. Typical continuous wave feed rates are about 100 inches per minute. Power and feed rate must be precisely balanced to achieve a weld with a specified depth of fusion. The slower the feed rate, the deeper the depth of melt and the more heat applied to the part.
Pulsed Laser Welding
Pulsed lasers produce a series of short pulses with a specific width and frequency. Pulsed lasers are capable of producing peak power above their average power because the energy is stored in a capacitor before being released. Pulsed lasers are capable of producing very high peak power: a 25 watt pulsed Nd:YAG laser can produce up to 5 kW of peak power in a few milliseconds. This means that it can perform spot welding that would require a 5 kW continuous wave laser!
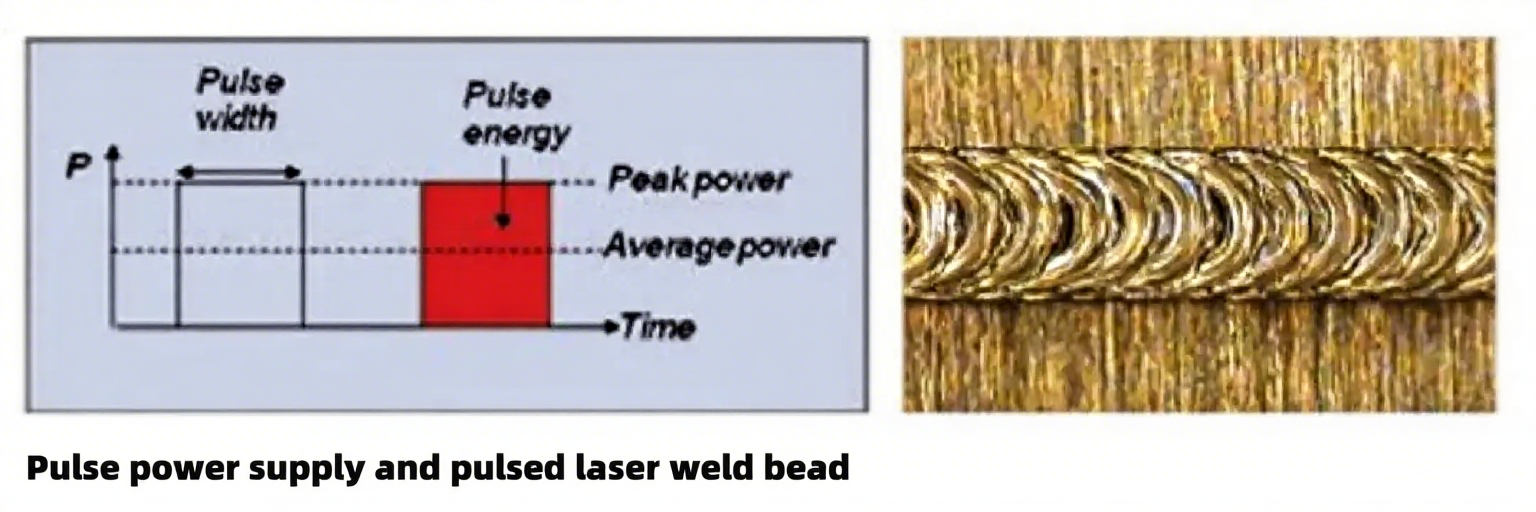
With a pulsed laser, a seam weld is formed by a series of overlapping spots. For hermetic sealing applications, the overlap of these spots is between 80% and 90%. For simple structural welds that do not require sealing, the overlap can be relaxed to around 70%.
Pulsed laser welding is recommended for heat sensitive parts and around very thin walled materials due to the short duration of the pulse (typically only a few milliseconds), which minimizes the amount of heat entering the part.
Pulsed laser welding is usually applied to highly reflective metals due to the extremely high energy at the beginning of the pulse. This peak power at the beginning of the pulse cycle is often referred to as the “enhancement pulse” and represents only a small fraction of the overall pulse duration. However, it is energetic enough to break through the reflectivity of the material while keeping the average power low, thus reducing heat. Continuous wave lasers must output a large amount of energy to couple with highly reflective metals, and the heat generated can easily damage the parts or components inside.
Both Continuous Wave (CW) lasers and Pulsed lasers offer distinct advantages and are best suited for specific applications. Continuous Wave lasers, with their high energy density and stable output, excel in deep penetration welding, high-speed operations, and joining materials with high thermal conductivity or reflectivity. Pulsed lasers, on the other hand, deliver controlled peak power and minimal heat input, making them ideal for precision components, heat-sensitive materials, and applications requiring hermetic sealing. In practical manufacturing, the choice between the two depends on factors such as material type, thickness, weld geometry requirements, and thermal management constraints. Understanding these differences not only enhances product quality and welding efficiency but also optimizes equipment investment and maintenance costs, providing a competitive edge in today’s demanding industrial landscape.