Shipbuilding industry has been known as “the crown of the comprehensive industry” title, its huge amount of steel and complex parts and components of the structure of the processing equipment puts forward a very high degree of precision, efficiency and stability requirements. With the continuous upgrading of manufacturing technology, 10,000-watt fiber laser cutting machine, by virtue of its high precision, high flexibility, high stability and other advantages, is gradually replacing the flame cutting, plasma cutting, waterjet cutting and other traditional processes, and has become one of the key technologies to promote the high-quality development of the shipbuilding industry.
Sheet metal for the marine industry,Analysis of the pain points of traditional cutting methods
In the manufacturing process of products in the shipping industry, about 70% of the hull structure consists of large-size steel plates and sections. Cargo ships, oil tankers, container ships and other large ships, for example, its deck, ribs, side plates and other key components used in the steel plate thickness is usually between 20 ~ 60mm, part of the thick plate to facilitate subsequent welding also need to beveling, complex process, the power of medium-thickness cutting equipment, precision and beveling ability to put forward very high requirements.
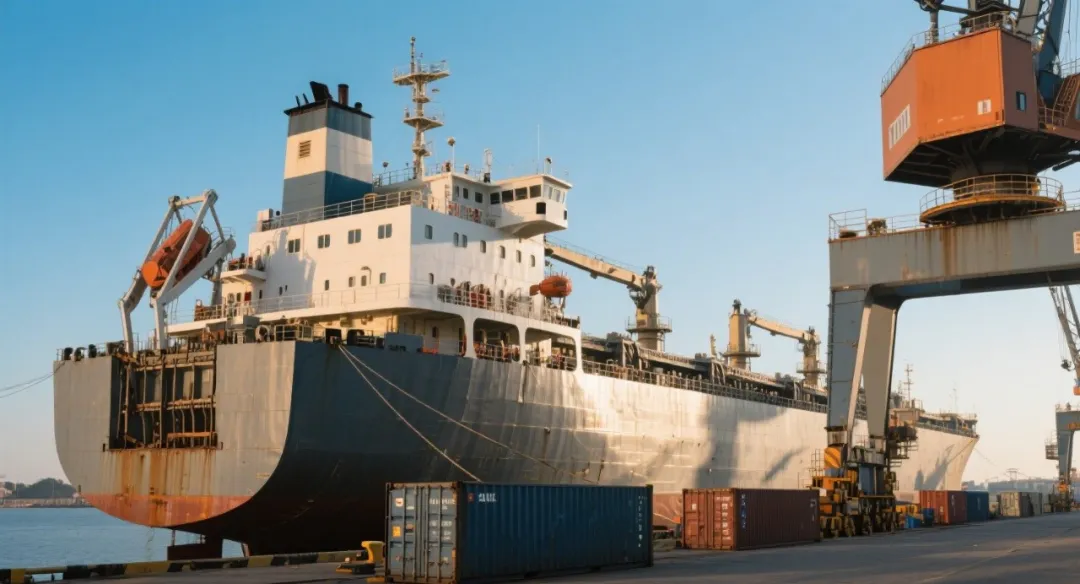
In the production process of the shipbuilding industry, the traditional processing methods of steel plate undercutting mainly include flame cutting, plasma cutting, waterjet cutting, shear processing, etc. The disadvantages are that the cutting gap is large, and there are a lot of slag and burrs. Its shortcomings are large cutting gap, slag, burrs, difficult to achieve high-precision processing of post-process welding, etc., requiring a large number of grinding and trimming, increasing man-hours; processing of heat-affected area is large, the cutting accuracy can not be guaranteed, especially in the field of small-hole cutting, complex graphic cutting is limited; electrodes, nozzles and other wear parts consumed quickly, long-term use of high cost; difficult to dock the modern intelligent manufacturing system; and poor flexibility, pollution, etc., which restricts the production capacity of batch shipbuilding and complex precision ship models.
Fiber Laser Cutting,Lean Shipbuilding and Fast Shipbuilding
10,000-watt fiber laser cutting technology for the marine industry is bringing unprecedented revolutionary changes in sheet metal processing. One of the most intuitive breakthroughs, is the continuous improvement of the thickness of the material can be processed, the market 10,000-watt fiber laser cutting machine is generally 12kW, 20kW, aluminum alloy cutting thickness of up to 40mm, stainless steel can reach up to 50mm. with the emergence of high-power lasers, a variety of metal plate cutting thickness and efficiency limits are being constantly refreshed.
In the shipbuilding industry, metal plate cutting has always been a key process to limit the efficiency and cost. Especially in the batch processing of 50mm and above carbon steel plate, the industry generally adopts 40kW, 60kW or even higher power lasers, which triggers large investment in processing equipment costs, high energy consumption, complex operation and maintenance, and has become the constraints on the threshold of the shipbuilding enterprises to reduce the cost of gain and upgrade the smart manufacturing.
Glorious Laser 30KW Fiber Laser Cutting
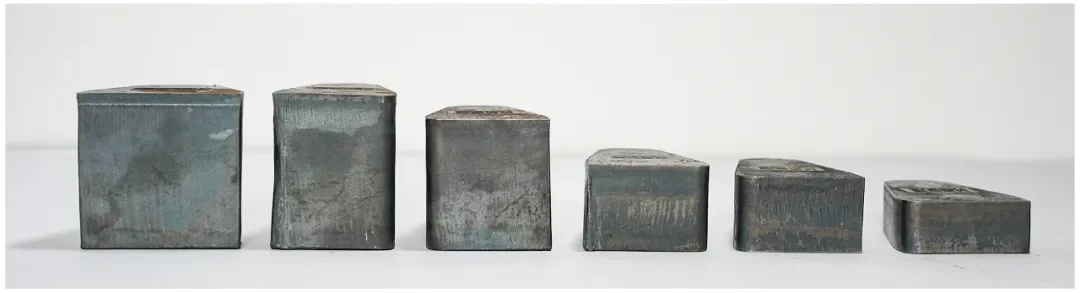
△Glorious Laser 30KW fiber laser cutting machine cutting sample display: carbon steel (70mm), carbon steel (60mm), carbon steel (40mm), carbon steel (35mm), carbon steel (25mm)
Glorious laser through the light source control, cutting head structure, process database, gas control and other technology synergistic upgrading, the first to solve the traditional high thickness metal plate laser cutting “can only rely on the pile of power” problem. In the field of carbon steel cutting, Glorious laser 30kW laser can realize 70mm carbon steel bright surface cutting, and can easily cut high thickness aluminum plate, brass and other high anti-materials.
Analysis of the core advantages of Glorious Laser 30KW fiber laser cutting process in the field of thick plate cutting in the marine industry:
- -Fast cutting speed of metal thick plate, short piercing time;
- -Good perpendicularity of the cut, no slag, no burr, no need for secondary grinding treatment;
- -Mature technology, low thermal load, high system stability, moderate requirements for cooling and beam transmission, and less post maintenance;
- -Satisfy most of the needs of thick plate processing, the shipbuilding industry can be fully competent for the routine application of thick plate cutting;
- -Moderate laser power, low energy consumption, more energy efficient, less burden on daily electricity costs;
- -Low investment in equipment cost and fast return on investment, which is very suitable for the marine industry’s demand for high-specification and batch steel plate processing and manufacturing.
Glorious Laser 10,000 Watt Fiber Laser Bevel Cutting
Hull steel plate can be roughly divided into the bottom plate, deck plate, side plate, bulkhead plate, etc., each part needs to be cut and molded independently, and then welded and assembled. In order to make the welding between the parts more solid, the steel plate needs to be beveled when cutting, and the quality of bevel cutting will directly affect the subsequent welding quality.
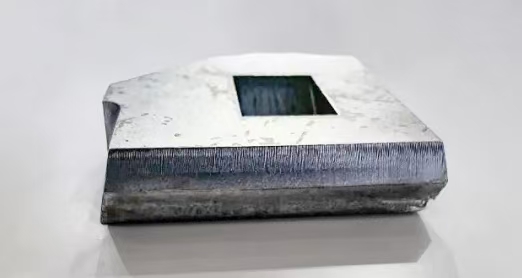
The bevel processing of traditional process requires cutting and then trimming the edge by hand and edge planer, which is time-consuming and labor-intensive. And 10,000-watt bevel laser cutting equipment through rapid programming and automatic nesting, biaxial swing is not less than ± 45 °, can quickly cut K-type, V-type, Y-type, U-type, X-type and other bevels, the cutting surface is smooth and fine, spliced with zero gap, to achieve high-quality bevel process precision machining.